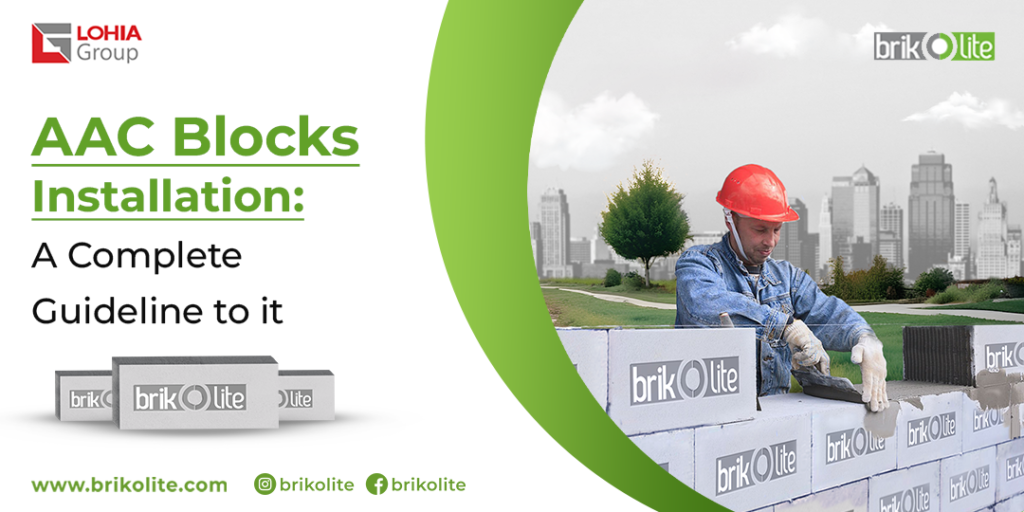
AAC Blocks Installation
Are you looking for a comprehensive guide to AAC block installation? This blog post is the perfect resource for anyone interested in learning more about the process of installing AAC blocks. Here, you can find out about the different types of AAC blocks, the tools needed for installation, the steps to follow, and the advantages of using AAC blocks.
Have a quick look at the AAC block installation guidelines for a smooth construction activity.
Setting up wall lines
One of the most important things to keep in mind during AAC block installation is the layout of your wall lines. This will ensure that your blocks are installed in a straight and level manner, which is essential for a professional-looking finish.
There are a few different ways that you can lay out your wall lines, but the most common is to use a string line. This involves attaching a string to two points on either side of the wall that you’re working on and then using it as a guide to make sure that your blocks are laid in a straight line.
Another method is to use chalk lines, which essentially work in the same way as string lines. The main difference is that chalk lines are easier to see, making them ideal for use on darker-colored AAC blocks. Whichever method you choose, make sure that you take your time when laying out your wall lines. A little bit of effort at this stage of AAC block installation will pay off in the long run.
As you work, keep an eye on your level to make sure that the blocks are being installed evenly. Once all of the blocks are in place, allow them to cure for 24 hours before grouting.
Working on the bed level
Create a deep joint of sand cement mortar at the maximum edge of the slab by drilling a 1/2-inch hole with a masonry trowel. Additionally, avoid using thin-bed mortar or mortar with large flakes when flattening the bed joint. Also, keep in mind to add the sand-cement mortar with a water-resistant composition if moisture and absorbency are the concerns. Last, but not least, make sure the top level of each block has the identical height.
Settle the first corner block
Place the first corner block in the sand-cement mortar and make the requisite modifications to the joint. Lessen or elevate the block to the desired height by striking it down with a rubber mallet or by adding more mortar underneath while following AAC block installation.
Using a 1/4-inch pointed trowel and thin-bed mortar, position the second corner block’s head joint. To establish an even height, duplicate the steps for individual edges employing a builder’s level. Also, each prime corner must be scrutinized three times in each plane.
Beyond the corner wall
The arrangement of the remaining walls comes after the corners have been put in place. Following that the blocks must be overlaid within the core area of other blocks. Within every five to six levels of blocks, a lentil must be integrated using only a 6-8 mm iron rod. The wall must then be perfectly measured for it to be thoroughly parallel to the ground.
Install lintels as needed
Placing of lintels is suggested with a standard rate of 8 inches (load) if applicable. Also, the lintels should have an 8″ minimum end tolerance. Concrete spreaders or pad stones should be used in situations where the pressure under the lintel bearing surpasses the acceptable levels such as under heavy intensive loads.
Appliances for AAC block installation.
The following tools aid in the proper AAC block fitting.
- Rubber Hammer or Rubber Mallet
- Notched Trowel
- Concrete Hand Saw
- Wall Chaser
- Bucket Trowel
- Grooving Tool
- Rubbing Tool
- Wire Brush
- Spirit Level
Adhere to the instructions listed below when using AAC blocks.
- Storage & Stacking – To prevent damage and interactions with dampness, store it on a smooth, dry surface.
- Mortar for masonry – The masonry mixture of cement and sand should always be kept at 1:6 ratio.
- Bond Pattern – A minimal 10 mm bearing spacing is necessary for joints.
- Wetting of Block before Application – Put the block completely underwater, and then remove it immediately.
- Mortar Thickness – Maintain a minimum mortar thickness of 10 to 12 mm.
- Mortar Joins – For accurate plaster-to-masonry bond strength, dented joints are advised.
- Coping Beam – The AAC blocks installation process remains incomplete without the placement of coping beams on the exterior walls. The coping beams provide support for the AAC blocks and help to distribute the weight of the blocks evenly.
The coping beam must be placed with 2 nos. of 8 mm reinforcement after 1.2 meters height each.
- Maximum Height of Wall Built in a Day – The wall height should be 6 Layers or 12 meters in a day. It should be done on dry and even surface to avoid damaged and contact with moisture.
- Electrical & Sanitary Chases – The chases should be installed before plastering. The depth of chases vertical should be less than 1/3 of wall thickness and horizontal depth should be less than 1/6 of wall thickness.
- Plastering Thickness – The External thickness of plastering should be 15 mm and 10 mm internally.
- Block Cutting – Use handy tools like hacksaw or rotary cutter for AAC block cutting for an even result.
- Curing of Masonry Wall – Do not cure like red clay bricks. Curing is required only for mortar joint.
- Lintel – It should be rest on full block and not half block.
- Chases Area – The chases area should be filled with compact mortar and then wire mesh should be applied.
Handling and proper AAC panel installation require professional assistance and expertise. Thus, sticking to the hinted guidelines is imperative for their firmness and tenacity.