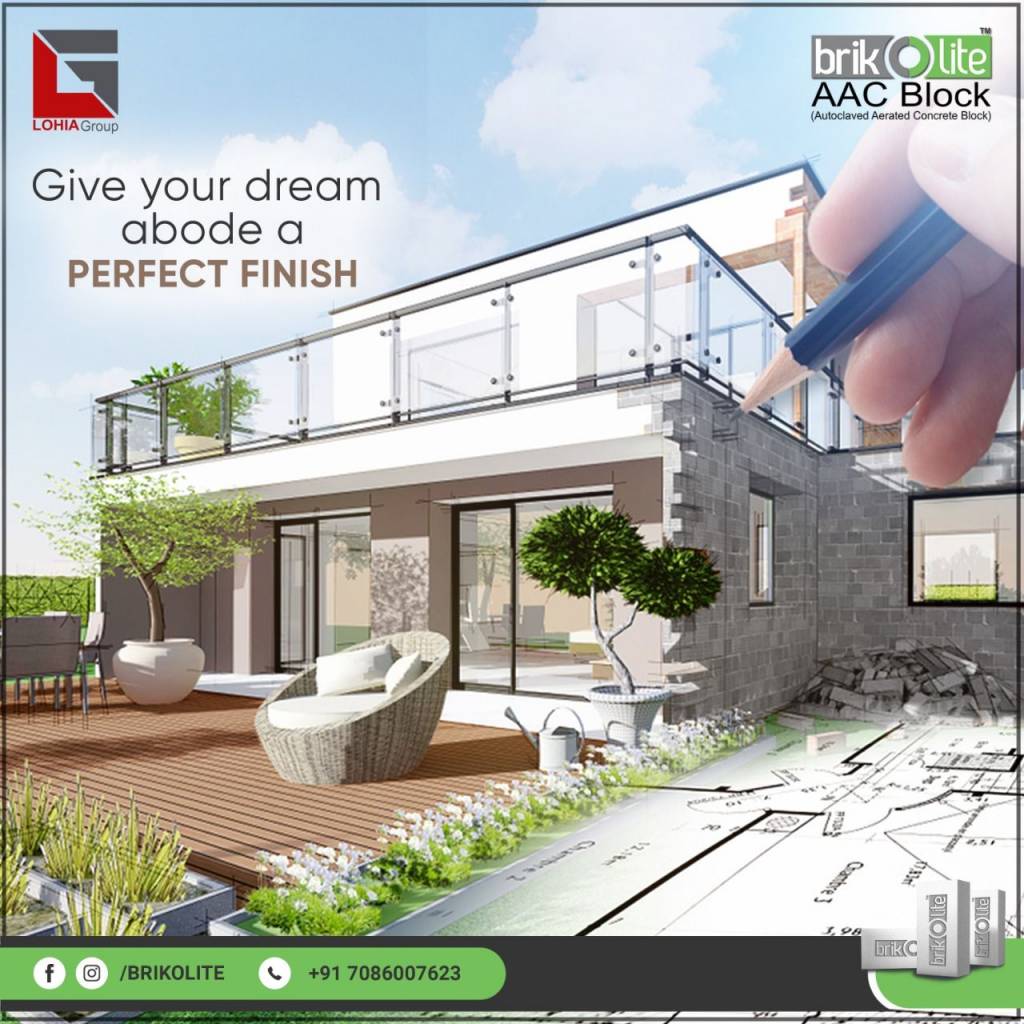
AAC or Autoclaved Aerated Concrete Blocks are becoming increasingly popular in the Indian market. In fact, India is considered the second largest block manufacturer in the world after China. As more and more undersized players are establishing plants to manufacture AAC blocks in India, the real question is – how are these blocks being manufactured?
We provide you with a detailed guide to what goes into making Brikolite AAC blocks and their process for manufacturing in bulk.
What are AAC Blocks?
In comparison to traditional red clay bricks, AAC blocks are lightweight yet sturdy in nature. They are highly insulated and made of cement-based recyclable materials including fly ash, gypsum, lime, water and aluminium powder, which is widely used as a foaming agent giving these bricks their portability.
AAC blocks are considered to be eco-friendly because of their ecologically neutral products. Moreover, since they are easier to use than red clay bricks, they are growing in demand in the Indian market.
How are AAC Blocks Made?
The manufacturing process of AAC Blocks is easily understood by laymen and it is easy to follow the procedure. It can be manufactured anywhere and at any place without significant investment because these blocks are easily available in the market.
The process for manufacturing AAC blocks is as follows,
- Preparing the Raw Material: Fly ash constitutes the base of AAC blocks. Since it is readily available as industrial waste, it is utilised in the mixture for manufacturing AAC Blocks. In the first step, all raw materials including recyclable ones like gypsum, aluminium powder and cement are put together in a doser.
- Dosing & Mixing Ingredients: Fly ash is then converted into a slurry and added to a mixing drum. The rest of the raw materials are added to the drum using screw conveyors. To ensure the right proportions are added during the mixing stage, automatic feeding systems are put in place. Once the ingredients are mixed thoroughly, they are ready to be added to the moulds.
- Moulding, Rising & Pre-curing: Each AAC block is made in a mould. These moulds are properly oiled to avoid any sticky material on the surface. The slurry is added to the moulds where aluminium reacts with lime and water to expand the slurry mixture. This is the rising process which makes the block lightweight. This is followed by a wire cutting process to ensure every AAC block is of the same height and width. After this process, the AAC blocks are pre-cured which takes anywhere between 1-3 hours depending on the weather conditions.
- Autoclaving: The last step in the manufacturing process is called autoclaving. Here, the AAC blocks are heated in an autoclaved chamber to increase durability and stability. This is carried out for 8-12 hours heating the blocks up to 180 degrees. Once done, the AAC blocks are transferred on pellets to the factory where quality tests are conducted to roll out the blocks into the market.
The Takeaway
When compared to conventional bricks, AAC blocks showcase maximum durability and efficiency and are hence the ideal choice for builders in India. If you’re looking for the perfect building material for your project, you should choose Brikolite AAC blocks for their successful completion.
1 Comment
sanjay Roy
Thank You sir, Good Information on AAC Blocks.
Comments are closed.